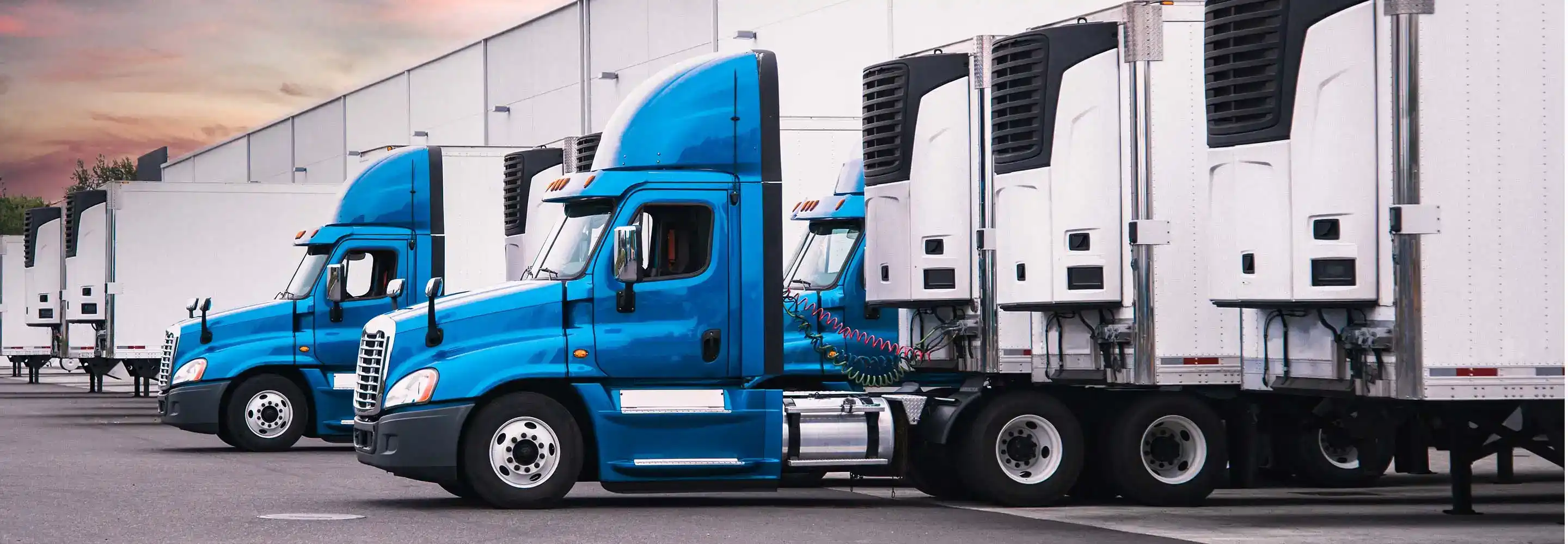
eBooks
Reefer Transport: 7 Key Challenges that can Cause Rejected Loads
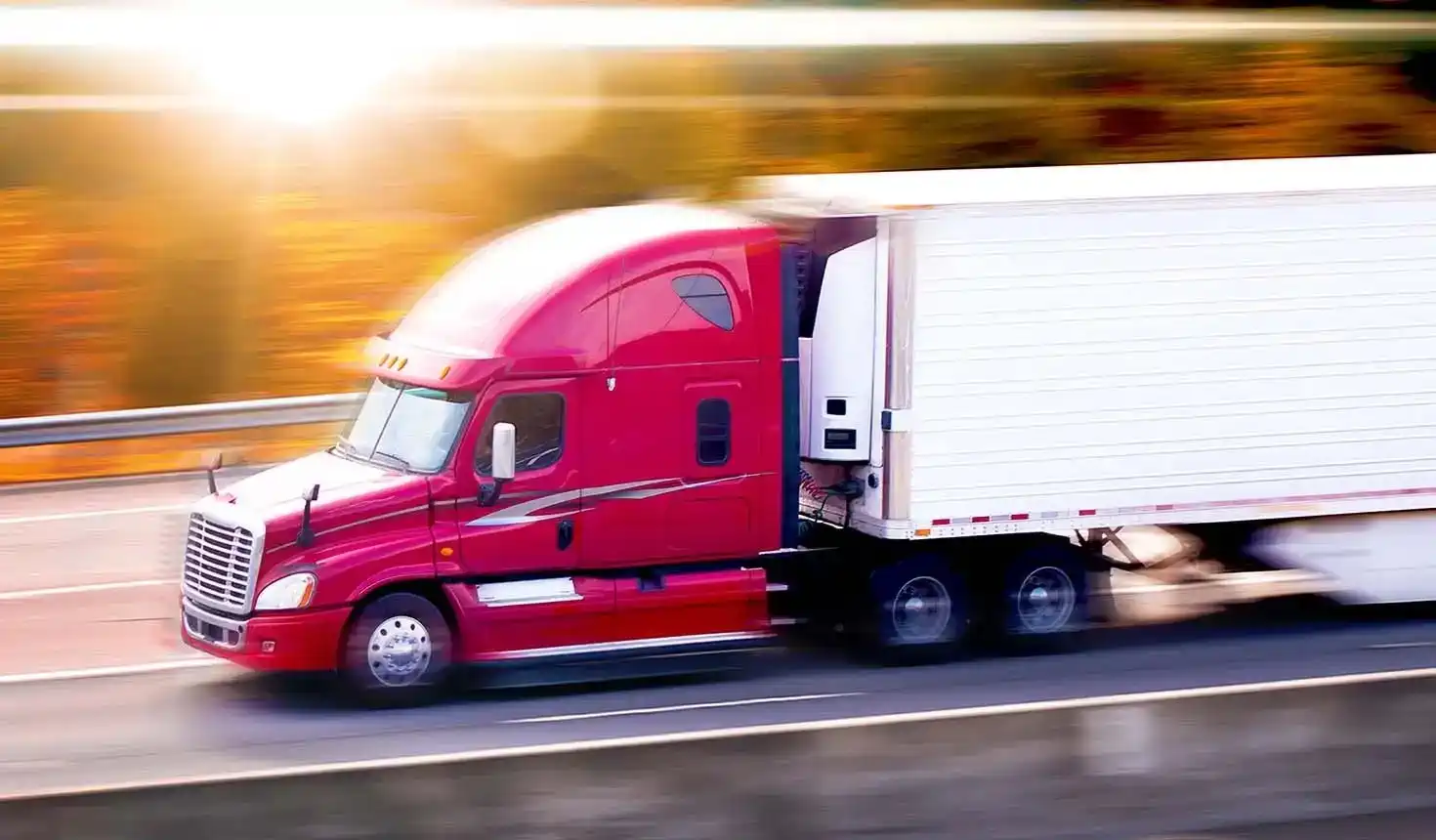
7 key challenges that can cause rejected loads
The problem of rejected loads
Failing to meet these challenges can lead to rejected loads. Delivering cargo at the wrong temperature can spiral into costs so significant they far outweigh the invoice value of the job. When a load is rejected:
- The transporter must compensate the shipper for the cargo, either by direct payment or through an insurance claim.
- The cargo must be disposed of in an environmentally friendly manner, which can be expensive for the transporter.
- If an insurance claim is paid out, the transporter can face an increase in premiums for years following the claim.
But the most significant cost is the damage to the transporter’s reputation. Losing one’s reputation as a quality service provider can result in a reduction of business. Reputation with a customer is built slowly, but it can be lost instantly with a single spoiled load.
Traditional avoidance methods
Many transporters try to mitigate the risks associated with refrigerated cargo by:
-
Renewing fleet equipment regularly:
The newer the equipment, the less likely it is to cause a problem. However, this adds complexity. Modern refrigeration units are complex and can have more than 200 fault or alarm codes. -
Training drivers:
Training drivers on best practices in refrigerated cargo handling and operation of the refrigeration unit is a proactive measure. But with increased driver turnover, a focus on driving more safely and increasingly complex refrigeration units, drivers have less time to spend managing their cargo temperatures. -
Using temperature dataloggers:
Dataloggers are useful tools for analysis and reporting, but they can’t see problems until the damage is already done. -
Paying insurance premiums:
Transportation owners spend a lot of money on insurance policies to protect their business in the event of an incident. But insurance doesn’t cover the loss of customer goodwill and the potential damage to your reputation as a transportation provider.
While these ideas are worthwhile and beneficial to an extent, they’re not enough to protect your business fully. In this document, we examine seven of the most significant and common challenges that carriers of temperature-sensitive products face today—hot loads, equipment failure, driver error, late notification of problems, providing proof after an incident, regulations compliance and lack of remote control—and what you can do to overcome them.
1. Hot loads
Industry analysts estimate that 32% of refrigerated cargo loaded onto refrigerated vehicles is at the wrong temperature at the time of loading. In most cases, the cargo is warmer than requirements dictate. The loss of temperature typically happens as a result of poor loading practices. The produce is left sitting too long on the loading dock before loading.
Unaware that the load is ‘hot’, or at the incorrect temperature, the transporter runs the risk of the load being rejected. It can mean a load claim and all the pain associated with it.
If the load is ‘hot’ at collection, most likely it’s going to be ‘hot’ at delivery. Many transporters believe the refrigeration unit will correct any discrepancy in loaded cargo temperatures. It might—but it will take a very long time if it manages it at all.
Refrigeration units aren’t designed to alter the temperature of the cargo, but to maintain it at the loaded temperature by cycling enough air to prevent further temperature loss.
Using advanced temperature monitoring can prevent hot loads by detecting a problem within 30 minutes of its occurrence. Automatic notifications go directly to the carrier, who can work on rectifying the situation.
2. Equipment failure
It’s a fact of life; sometimes equipment can break down. It’s the same with refrigeration units. If a reefer unit fails, the potential of your entire shipment or order can fail.
In the event of a breakdown, knowing about it is as good as being able to fix it. Installing active alarms can help to combat the damages caused by reefer equipment failure. These signal directly to the back office in the event of a malfunction. The dispatcher can look at addressing the issue and advise the driver, who can remedy the situation from where they are.
3. Driver error
Modern refrigeration units can have over 200 alarm codes. That’s 200 potential problems that can threaten assets. Even if drivers spent hours each day reviewing information booklets, they probably still wouldn’t be familiar with every make and model of reefer unit available. Drivers already carry a lot of responsibility for staying safe and timely on the roads, without studying manuals for reefer units.
Automatic error detection systems can prevent driver error. Continuous reports send status information to the back office, which can track and identify any problems. Human error can play a part in the transportation process, and this can expose the carrier to the risks of driver mistakes.
A driver, for example, could change a setpoint to -2°C instead of –20°C. This could be disastrous for the cargo, making the entire load unusable. This will be identified in reports to the back office through automatic error detection.
4. Late notification
Timing is key for temperature-sensitive cargo like fruit, vegetables, or pharmaceutical products. Saving a load after the fact is one thing but being able to rectify the situation before the problem occurs is another entirely. Hauliers need to be able to identify issues before they crop up. Real-time data with immediate notifications help to stop hot loads in their tracks.
Real-time cargo temperature monitoring can give early warnings of any issues. These solutions are configurable to the type of cargo and carriers can set variations based on the tolerance level of the produce. Notifications are instant for ‘out-of-range’ temperature conditions with comprehensive reporting of sensors. It removes the responsibility from the driver, who has little visibility of the controller when on the move. Four hours could go by before a driver inspects the trailer and by then it will be too late to save the load.
5. Immediate proof on delivery
If something does go wrong, the driver or carrier is usually the first one to get the blame. If things do go wrong, carriers need evidence to back up the conditions of the transported cargo. Compliance, auditing and documentation are vital for each refrigerated unit.
If a temperature query occurs, temperature monitoring solutions provide proof of in-transit monitoring and consistent vehicle updates. The information is instantly delivered to the shipper or receiver to avoid extra costs or possible disruption.
6. Regulatory compliance
Regulations on this theme are only set to increase and become more stringent to ensure clear audit trails in the event of a temperature problem. Transportation companies are impacted regularly with the implementation of new rules aimed at keeping the food supply chain safe.
Carriers can ensure compliance by improving procedures, implementing the correct monitoring technology and training drivers in temperature and record management for each shipment. This ensures cargo is protected in real-time with an audit trail to prove it.
7. Lack of control from head office
New regulations can introduce complex systems and procedures. Compartmentalised vehicles, multitemperature, multi-zone loads can be difficult for drivers who may not have the experience or skills to monitor, analyse and fix temperature problems. There are enough distractions for drivers on the road without having to worry about fixing an accidental defrost. This is when remote, two-way control can and does save the day.
Temperature management systems allow approved users two-way reefer unit control in the event of an issue. Remote control features include switching the reefer on and off, defrost initiation, clearing alarms or changing the mode of operation from any location any time.
The 7 challenges discussed here are real concerns for refrigerated transport owners. ORBCOMM’s cold chain solutions afford you full protection. By providing complete control of the environment—in real-time, remotely, on any device and from any browser—we protect your temperature-sensitive cargo, reduce your business risks and deliver perishable products safely, on-time and in compliance with rules and regulations.
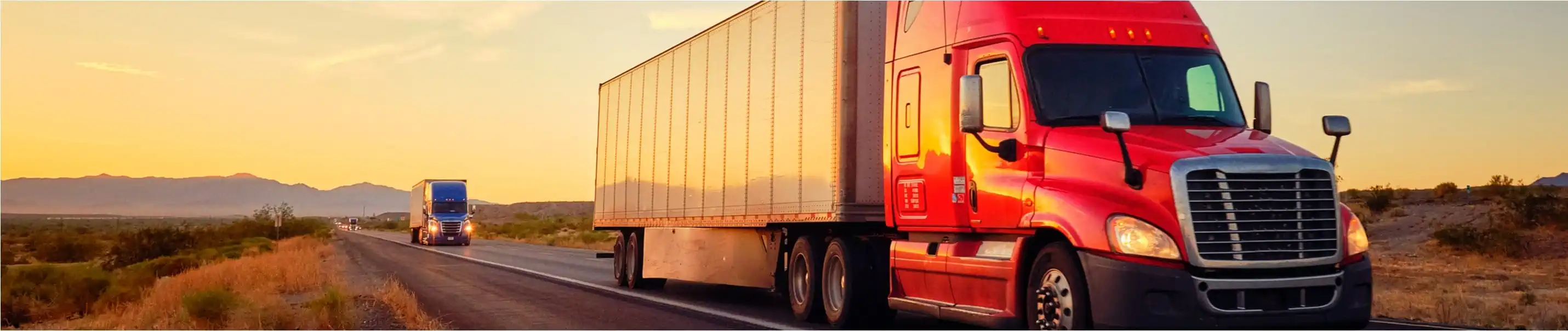